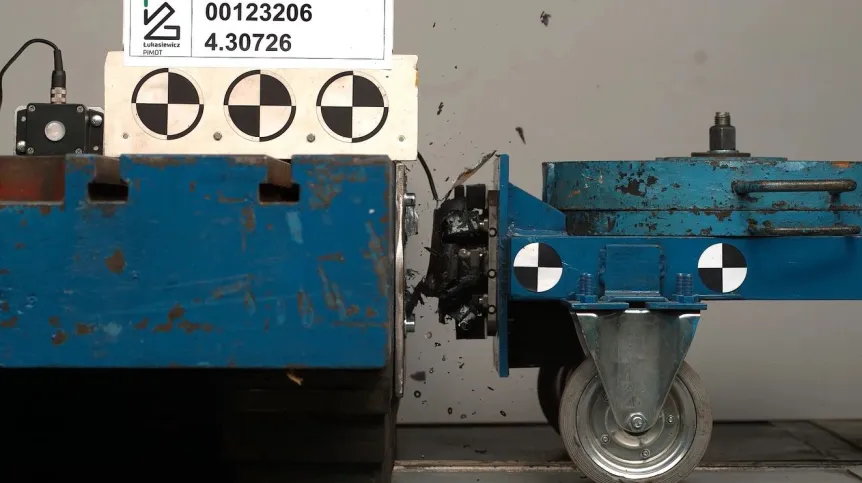
Energy absorbers absorb the kinetic energy of accidents, collisions and falls to protect passengers and vehicles. Researchers from Warsaw have developed cheap absorbers made of innovative composite materials, which can be used, for example, to build airline seats and airplane floors, as well as crash boxes in cars.
Representatives of the Łukasiewicz Research Network reported on the research project in a press release.
A method for producing impact energy absorbers based on a carbon composite with a thermoplastic binder was developed by Adrian Lipkowski, currently affiliated with the Łukasiewicz Research Network - Institute of Aviation. In December, his diploma project on the topic, prepared as part of his studies at the Warsaw University of Technology, took first place in the competition of the Polish Union of Plastics Converters for the best diploma project.
In a review of the project, Krzysztof Pieńkowski from the Polish Union of Plastics Converters wrote that absorbers made of thermoplastic materials 'are much lighter than widely used hydraulic and friction absorbers. This reduces the weight of the object involved in the collision, which further reduces its kinetic energy.’
Representatives of the Łukasiewicz Research Network hope that the technology will be used in the aviation industry in the production of aircraft seats, aircraft floors and landing gear, as well as in the automotive industry, primarily in the front and rear crash boxes (located in front of the bumper and attached to the chassis) in cars.
Research for the engineering project was carried out as part of the frontal collision energy absorber for a passenger vehicle (CRASH-BOX) project, which was financed by the Łukasiewicz Research Network. The leader of the consortium was Łukasiewicz Research Network - Automotive Industry Institute, which conducted crash tests. The Łukasiewicz Research Network - Institute of Aviation, whose experts specialize in composite technologies, also participated in the project.
'The key features of this technology, in addition to weight reduction, include fast production, a wide range of available materials, tailored design, corrosion resistance, integration and production efficiency, as well as the possibility of recycling,’ the Łukasiewicz Research Network researchers say. (PAP)
PAP - Science in Poland
lt/ bar/ kap/
tr. RL