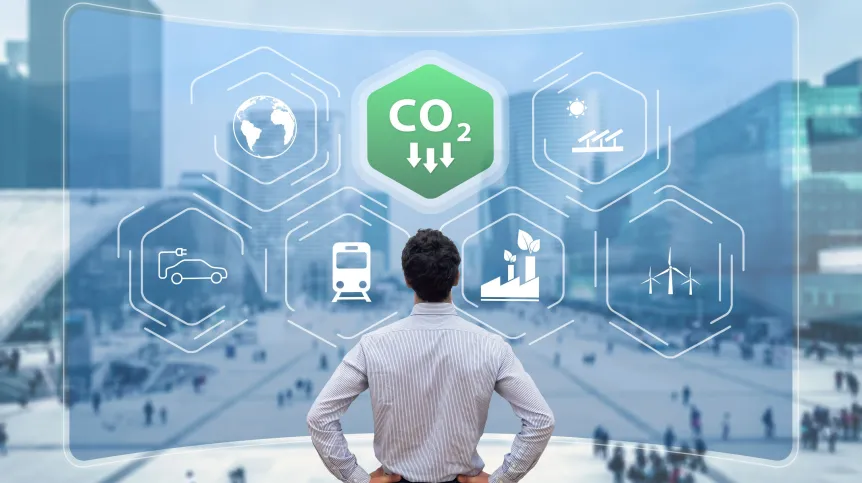
A Polish-Japanese team is working on a chemical reactor that will convert carbon dioxide emitted by small boilers into methane suitable for use as fuel, reports the Journal of CO2 Utilization.
Small fuel combustion sources such as boilers and other industrial devices are responsible for a significant part of greenhouse gas emissions. Boilers are widely used across various industries for essential processes such as heating, steam generation, and power production.
The designs of most boilers are so refined that it is difficult to reduce CO2 emissions simply by improving combustion efficiency. However, a promising direction seems to be capturing CO2 emitted during the combustion process and converting it into a useful product, for example methane.
A specific type of membrane reactor is needed for this, called the distributor-type membrane reactor (DMR). It can facilitate chemical reactions as well as separate gases.
While DMRs are used in certain industries, their application for converting CO2 into methane, especially in small-scale systems like boilers, has remained relatively unexplored.
The teams led by Professor Grzegorz Brus from the AGH University of Science and Technology in Kraków and Professor Mikihiro Nomura from the Shibaura Institute of Technology in Tokyo (Japan) have been working on filling this gap.
The team used numerical simulations and experimental studies to optimise the reactor designs for efficient conversion of CO2 into methane. In their simulation modelled gas flow and reactions under different conditions. This, in turn, enabled the researchers to minimise the temperature variations, ensuring optimised energy consumption during methane production.
It turns out that, unlike in traditional methods that channel gases into a single location, a distributed feed design is more beneficial. It makes it possible to spread the gases out into the reactor, resulting in a better distribution of CO2 throughout the membrane and preventing local overheating. 'This DMR design helped us reduce temperature increments by about 300 degrees compared to the traditional packed bed reactor', says Professor Mikihiro Nomura.
In addition to the distributed feed design, the researchers also explored other factors influencing reactor efficiency and discovered that one key variable was the CO2 concentration in the mixture. 'When the CO2 concentration was around 15%, similar to what comes out of the boilers, the reactor was much better at producing methane. In fact, it could produce about 1.5 times more methane compared to a regular reactor that only had pure CO2 to work with', Nomura adds.
The scientists also investigated the impact of reactor size. They found that increasing the size of the reactor improved the availability of hydrogen for the reaction. However, the benefit of higher hydrogen availability requires careful temperature management to avoid overheating.
According to the authors of the study, the benefits of converting CO2 into methane could be obtained, for example, in home installations and small factories. (PAP)
Paweł Wernicki
pmw/ agt/ kap/
tr. RL