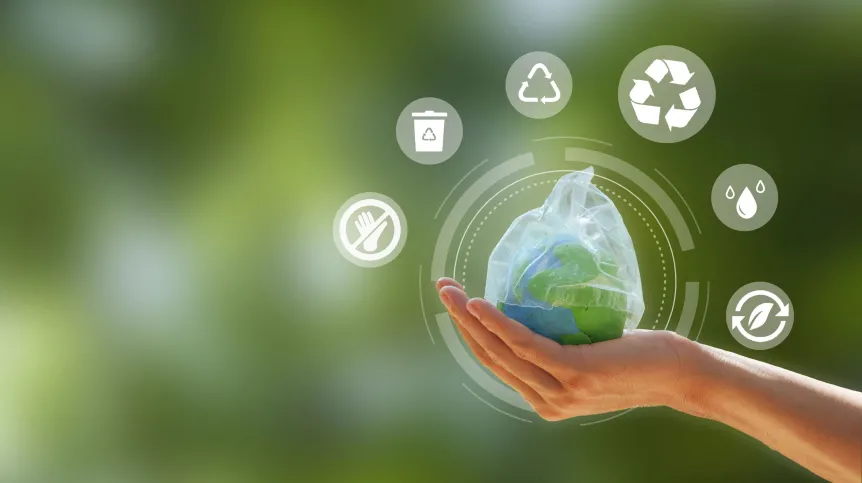
Recycling plastics is a necessity, which is why scientists keep looking for better solutions. As part of a grant awarded by the Polish National Science Centre, a team from the Silesian University of Technology is working on a nearly 100 percent effective method of processing composite materials.
The main goal of the project is to develop an innovative and environmentally friendly method of disposing of problematic plastic waste and waste composite materials (with heterogeneous structures), which currently can only be landfilled or incinerated.
Project manager Professor Sebastian Werle from the Faculty of Energy and Environmental Engineering of the Silesian University of Technology said: “Thanks to this solution, it will be possible to not only dispose of waste, but also recover very valuable fibres (carbon or glass) used in the production of plastics, and organic chemical compounds, such as carboxylic acids or volatile fatty acids, which can be raw materials for the chemical industry.”
Werle added that one of the most important aspects of the new method is that it is almost 100 percent effective - it enables nearly 100 percent conversion of plastic materials into an aqueous solution in a relatively short time.
He said: “In addition, the process does not use organic solvents, which reduces the negative impact on the environment and the health of the workers who control the process. Thanks to the use of water as the process medium, the risk of fire, always present in other methods of thermal waste treatment, is eliminated. In addition, unlike other methods of thermal processing of plastic waste, where moisture in the waste affects the profitability of its processing, in our solution the moisture is not an obstacle. This is especially important because obtaining dry waste is time-consuming and expensive, which may affect the profitability of classic waste disposal processes.”
Although the method proposed by his team seems similar to combustion, because the oxidation of the organic matrix also occurs in this case, there are no products of classical combustion.
Werle said: “Instead, the main products are carboxylic acids and volatile fatty acids. The method consists in oxidative (in the presence of oxidants) liquefaction of plastics in the presence of an aqueous solution of dihydrogen peroxide at an elevated temperature of 250-300 degrees C and increased pressure (100-150 bar). Under such conditions, long polymer chains are broken down into smaller components, which are then oxidized to carboxylic acids and volatile fatty acids.”
According to Werle, his team's method of oxidative liquefaction of waste plastics and waste composite materials is 'an alternative and unique solution that responds to current social and environmental problems'.
He said: “The idea for it was born from the need to change and reduce energy and environmental costs that we are currently facing around the world.”
The project also includes the implementation of multidimensional data analysis. Professor Werle explained that this includes the methods of chemometric analysis that not only determine the main variables affecting the studied process, but also provide answers to the question of whether there are other significant variables or interactions affecting the quality of the obtained products
The research is carried out in the project 'Oxidative liquefaction of plastic waste. Experimental research with multidimensional data analysis using chemometric methods', financed by the National Science Centre in the OPUS competition. The project started a year ago and is expected to continue until 2025.
The research team members are: Professor Eng. Sebastian Werle (principal investigator), Dr. Szymon Sobek, Dr. Marcin Sajdak, Dr. Roksana Muzyka (post doc), Hamza Mumtaz (scholarship holder). The project is being carried out at the Faculty of Energy and Environmental Engineering of the Silesian University of Technology, in three Departments: Thermal Technology, Air Protection, and Heating, Ventilation and Dust Removal Technology. (PAP)
PAP - Science in Poland, Agnieszka Kliks-Pudlik
akp/ bar/ kap/
tr. RL