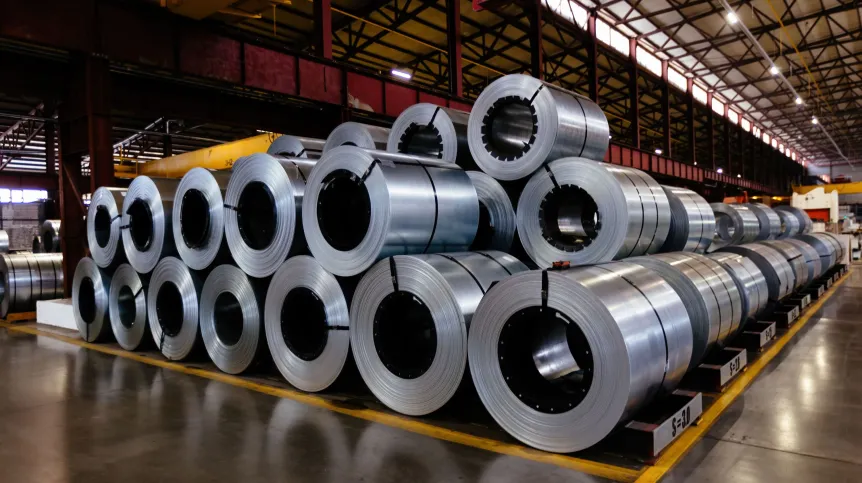
A new method of coating materials with thin layers in a way that resembles printing has been developed at the Jagiellonian University. It requires a minimal amount of chemical materials and can accelerate the development of 3rd generation organic solar cells.
According to the university, the technology enables the use of electrolysis without the need to immerse the coated objects in solutions. As a result, many materials can be coated with a variety of substances. The method makes it possible to manage the operation of the electrodes in such a way that coating the surface resembles printing. It is possible to create specific images, patterns or lines, as well as precisely adjust the thickness of the coating layer covering a given material - the thickness of the layers is counted in nanometers.
ECOLOGICAL ELECTROLYSIS
Electrodeposition is a process of coating various types of surfaces with a thin layer of a specific substance by means of chemical reactions. This makes it possible to protect materials from corrosion, obtaining surfaces with desired electrical conductivity properties, and improve or change the aesthetic features of materials.
Currently used electrolytic deposition methods consume a large amount of resources, which makes them both expensive and environmentally unfriendly. The researchers’ new method requires electrolytes in such small amounts that their cost becomes negligible.
'In commonly used electroplating methods, the coated materials must be completely immersed in the electrolyte, which significantly increases the costs. Our method completely breaks this rule. We have proven that electrodeposition can be performed almost dry, with a negligible amount of electrolyte, i.e. without immersing the objects in solutions. We only need to create a meniscus of electrolyte that will fill the space between the coated substrate and the cylinder-like mobile head with electrodes. Using this method, we can coat materials equally effectively without the need to use such large amounts of resources', explains the creator of the new method, says Professor Jakub Rysz from the Faculty of Physics, Astronomy and Applied Computer Science of the Jagiellonian University.
The professor explains that small amount of electrolyte is introduced between the coated surface and the head, placed closer than one millimetre to it. The electrolyte forms a meniscus no wider than a few millimetres. The liquid fills the space between the head with electrodes and the surface. The meniscus and the head can be moved on the coated surface during the electrodeposition process. The control system is supported by electrolyte dispensers and suction pumps working within the head. This enables the use of a minimal amount of the solution, as it remains in the head operation zone, on a relatively small surface. The electrolyte can be replenished or replaced during the operation of the electrodes, which means that the procedure can be carried out on larger surfaces.
AS PRECISE AS PRINTING
Using a movable meniscus on the coated surface and a movable head with electrodes opens up new possibilities in electrodeposition work. It is possible to control the applied voltage or the speed of movement of the meniscus. This means that it is possible to create new patterns from the material applied to the surface and adjust the thickness of its layer. The new method is similar to printing on a sheet of paper or painting, where you can decide how thick a layer of paint should be that covers the surface.
The method can also be enhanced with photodeposition. 'By applying different potentials in the electrode, we can cover some areas of the substrate with thinner layers of coating, other areas with thicker ones, and others we can keep without coating. There is a certain minimum margin related to the phenomenon of diffusion and printing in electrolysis is not as precise as material processing using CNC machines, but it provides very wide possibilities for managing the printing process. In addition, the industry has a wide range of substrates and coating materials at its disposal', says Professor Rysz.
INDUSTRIAL APPLICATIONS AND PROTECTION
The new technology enables coating materials with various metals classically used in galvanization - metal oxides with semiconductor properties, such as zinc, titanium or molybdenum oxide, as well as polymeric materials.
The Jagiellonian University physicists have developed many coating techniques based not only on electrolysis, but also on photodeposition using laser light beams. In the latter case, the coated substrates do not have to have conductive properties.
'Using the photodeposition technique, we can cover, for example, glass or ceramic surfaces with thin layers of precious metals. We can also draw specific paths, patterns or lines on the substrates, selecting both the type of coated material and the type of coating. By working with metal oxides, we can produce electrochromic glass, which darkens under the influence of applied voltage or sunlight. It is also possible to produce substrates with a larger surface area, which are needed in innovative, 3rd generation organic solar cells', says Professor Rysz.
In the future, this method may be used to produce photo catalysers for large surfaces, specialist panes, to precisely apply of metallic tracks on substrates (used e.g. in heated glass), including, of course, tracks made of precious metals, which require minimal raw material consumption due to their high value.
It is also possible to use the new technology to produce modern, thin and elastic solar cells. The scientists also think that it will find use in such future technologies as smart films and other materials covered with microsensors, or the production of materials coated with precious metal nanoparticles.
The invention is covered by patent protection in Poland and abroad, which means that it can be licensed. The scientific team also provides assistance at the stage of implementing the technology on an industrial scale. Tests of two head system prototypes confirm that the new technology can be used on both small and large surfaces.
PAP - Science in Poland
kol/ zan/ kap/
tr. RL