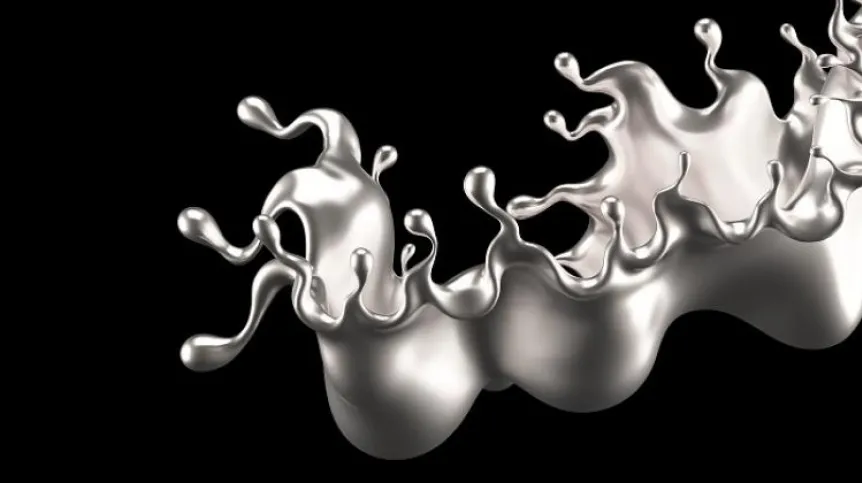
“Any sufficiently advanced technology is indistinguishable from magic” (Arthur C. Clarke). Researchers are working on a shape-shifting robotic material able to transform into any object or machine. Strong like solids and transformable like fluids, will T-1000 terminators knock on our doors soon?
Authors: Jakub Lengiewicz, Paweł Hołobut form Institute of Fundamental Technological Research of the Polish Academy of Sciences (IPPT PAN)
Shape-shifting creatures and machines have been subjects of sci-fi literature and movies for decades. Notable literary examples can be found in the works of Stanisław Lem (Invincible (1963), Peace on Earth (1985), Fiasco (1987)), who pursued this topic throughout his writing career. Arguably, the most evocative cinematic depiction of a shape-shifting material remains the T-1000 robot from the 1991 film Terminator 2, while the 2014 film Big Hero 6 shows a more detailed vision of how such a material/device could be constructed. In the majority of examples, the superior capabilities of shape-shifters are their adaptability to external environments or tasks and their tolerance to damage.
Fig. 1 Shape-shifting: a cup turns into a plate. Courtesy of Prof. Julien Bourgeois and Prof. Benoît Piranda, UBFC, FEMTO-ST Institute, CNRS.
But what do we really mean by a shape-shifting material? When we say “material” we have in mind something apparently continuous, like metal, clay or water. When we say “shape-shifting” we mean transformations unknown from common experience and seemingly contradicting the laws of physics. Like spilled water flowing back into a cup, a lump of clay shaping itself into a pot, or a metal ball spontaneously melting, forming a cube and solidifying again.
The foreseeable application domains of shape-shifters seem as futuristic as the technology itself. Try to imagine a future Skype in which you can shake hands with your peers, or a computer game in which you can physically interact with reproduced real-life versions of virtual characters or with avatars of other online players. In medicine, a shape-shifting material could be injected into the bloodstream, adapt to physiological conditions, enter target organs and treat or enhance them. Such adaptable, multi-functional, shape-shifting devices are indeed exciting prospects which could change the way we interact with the world. Yet they are still in their infancy, and we do not even know which of the potential applications are actually achievable. The fact is that the worldwide race to develop shape-shifters has already started, inspiring fascinating areas of research.
Robots made of robots
Shape-shifters cannot be made of any standard material. Atoms building ordinary matter are “passive” - they have no “will” of their own. Shape change of an everyday object can only be achieved by external intervention, like shaping a piece of plasticine in hands or melting wax by heating. Such manipulation of shape is very limited and is not what one has in mind when thinking about shape-shifting materials. One way of realizing true shape-shifting objects is to build them of artificial “atoms” which are active. Ones which can move on their own.
Such “active atoms” must have several capabilities. First of all, they should be able to propel themselves, e.g., “walk” on their colleagues. Second, they must “see”. They should have at least a rudimentary idea of what is happening around them. For that purpose they need to talk to their neighbors and perhaps observe the world through other simple senses. Third, they must “think”. Once they receive information, they need to analyze it and act accordingly using basic intelligence. Finally, they need energy. So they must carry small batteries or derive energy directly from the environment. Each “active atom”, or “module” as we shall call them, is thus a robot. A shape-shifting material is a robot made of robots.
Biology knows systems of this kind. They are not as advanced as the sci-fi imaginings, in fact they are rather slow and have limited functionality, but embody the general idea. One such natural system is fire-ants, which can build structures from their bodies to address challenges facing a colony. They form rafts to survive floods, bridges to cross gaps, towers and ropes to traverse vertical distance, and sometimes other “engineering” structures. Another example is cellular slime molds - unicellular organisms which live separately, but sometimes come together and act as a unity. They move over the ground as a slug, then settle down and form a mushroom, behaving as one multicellular organism. Both examples can be viewed as assemblies of “biological robots”.
The ambitions of creators of artificial shape-shifters reach far beyond what nature has produced. However, the results achieved so far fall short of expectations. We will try to present some of the problems as we proceed. Overcoming them is a major scientific challenge and an inviting field of investigation.
A chain is only as strong as its weakest link
The “body” of a robotic shape-shifter is built of modules. There are endless possibilities for what modules can look like and how they can move. Scientists have proposed many designs. For instance, Telecubes (Palo Alto Research Laboratory) are cubic blocks which attach side to side: they can protract and retract all sides so that they can push themselves away from or pull themselves towards neighbor blocks (Fig. 2, left). Another example is Catoms (Carnegie Mellon, Intel Corporation, FEMTO-ST Institute/CNRS): their surfaces are lined with controllable magnets or electric plates - electromagnetic forces of attraction or repulsion between adjacent modules cause them to bond or roll one over another (Fig. 2, right). It is still uncertain what designs will be miniaturized to the size of a grain of sand and form ensembles made of millions of modules.
Fig. 2 Telecubes (left) and Catoms (right). The authors’ own drawing.
To make a shape-shifter change its shape or position, all its modules must be told how to move. This motion, called reconfiguration, faces many difficulties in large groups of modules. For example, let us consider a random mass of modules resembling a pile of sand. The modules inside the pile and especially those at its bottom will find it difficult to move, because they carry the weight of the modules above them and will often be unable to push through using their limited-strength motors. In most cases, the modules will only be able to move over the surface of the pile. Such movement allows shape change, but at a very slow pace. It is similar to how dunes travel in the desert: wind blows sand from one side of the dune to another, inducing a very slow motion of the entire mass. To accelerate shape-change, more widespread motion of modules is required.
What can modules do to improve their collective abilities? The novel approach pursued at the Institute of Fundamental Technological Research of the Polish Academy of Sciences (IPPT PAN) is to organize the microscopic robots into useful evolving structures, similar to living tissues made of cells. Structurization of this kind makes a modular robot resemble more a traditional robot or an organism with its specialized organs. Here, however, the organs can disassemble after serving their function and then form something new. Below we show two especially useful types of such organization.
The first type addresses the problem of the weakness of individual modules in relation to the weight of the entire modular structure. The basic concept is to build a sort of artificial muscles which we call “volumetric actuators”. They have the characteristic feature that, under certain conditions, they can produce forces which are significant compared with the weight of the entire modular structure. This is because they aggregate tiny forces produced by individual “active” modules distributed throughout their volumes into one large output force. A design of this kind built of spherical modules is presented in Fig. 3: red and yellow “active” modules induce relative motion of the blue and gray frames.
Fig. 3 Linear volumetric actuator. The authors’ own unpublished work.
The second form of organization allows acceleration of shape-shifting by parallelizing the modules’ movement as far as possible. For this purpose, the robot’s body is made porous by design. During reconfiguration, modules flow from one end of the robot to another through the robot’s entire volume (like water through a sponge), instead of over its surface (like sand over dunes). One of such structures is presented in Fig. 4 (left), with gray modules forming a porous skeleton and red modules ready to travel. A special computer algorithm is used to plan organized, collision-free movement of modules along “flow lines” like the one in Fig. 4 (right). An example of shape change is shown in Fig. 5, with white lines with arrows designating flow lines.
Fig. 4 Special porous structure made of spherical modules (left) and a line of modules moving through the structure (right). From J. Lengiewicz, P. Hołobut, Autonomous Robots 43, 97–122 (2019), (CC BY 4.0).
Fig. 5 Example reconfiguration: the initial structure “flows” into the target shape. From J. Lengiewicz, P. Hołobut, Autonomous Robots 43, 97–122 (2019), supplementary materials, (CC BY 4.0).
Chitchat causing a global effect
Ordinary robots, as well as higher-order animals, have specialized organs for thinking - central processors or brains. Special message-passing channels, like nerves, communicate the brain’s decisions to muscles/actuators which act in response. A modular robot, as a whole, is different. There is no central brain, there are no nerves, there are no dedicated muscles. The entire body of a modular robot is also its brain. A brain whose neurons (modules) constantly move, making collective operation more challenging. The modules must constantly talk to each other, particularly to their neighbors, and collectively decide what to do.
One example of collective decision-making was shown in Fig. 5, where the flow lines were constructed by neighbor modules negotiating the best global solution. Another example concerns mechanical stability of modular structures. When shape-shifting proceeds, the structure may experience a mechanical failure. Just like any other structure, the modular robot may break or turn over if it is not properly balanced. To avoid such situations, the modules must be able to collectively predict dangerous moves.
In collaboration with the FEMTO-ST Institute in France and the University of Luxembourg, we have proposed a computational approach to this problem. The modules first form in their collective memory a mathematical model of their own configuration one move ahead. From this model they infer, by repeatedly talking to each other, if the altered structure will fail or not. The whole process is similar to how engineers analyze the strength of structures they design, with the distinction that modules analyze their own configurations by themselves. Examples are shown in Figs. 6 and 7, where modules predict possible overloading.
Fig. 6 Modules predict possible breakage after addition of new modules; red indicates expected failure. Top row: simulations in the VisibleSim simulator. Bottom row: experiments on the Blinky Blocks robotic modules. Courtesy of Prof. Julien Bourgeois and Prof. Benoît Piranda, UBFC, FEMTO-ST Institute, CNRS.
Fig. 7 Modules compute stresses at inter-modular connections; red indicates expected failure. Simulation in the VisibleSim simulator. The authors’ own unpublished work.
T-1000 terminator not in the near future
There are a number of obstacles to the development of advanced shape-shifters. First, current hardware designs of modules are deficient in terms of: shapes, which may not be well suited to fast reconfiguration, motors, which seem too weak to give the structure sufficient strength, and size, which needs to be significantly reduced. Second, reconfiguration and communication require vast amounts of energy, which should be derived from the modules’ internal batteries or harvested from the environment. Currently, these energy demands seem to prohibit stand-alone operation for extended periods of time. Finally, current software does not offer rapid reconfiguration planning. Distributed artificial intelligence algorithms, which would potentially control the entire complex behavior of a shape-shifting robot, are obviously even less advanced.
Overall, science fiction-type shape-shifting robots should not be expected anytime soon. This is both good and bad news, depending on one’s view on technology - subjectively, and on the ratio of benefits to dangers - objectively. We may also be wrong and some technological or conceptual breakthrough may allow the emergence of movie-type fluid robots in the near future - who knows? We keep working on them.
Jakub Lengiewicz, Paweł Hołobut
References:
- S.C. Goldstein, J.D. Campbell, and T.C. Mowry, Programmable matter, IEEE Computer, vol.38, no.6, pp.99–101, 2005.
- Claytronics Physical Dynamic Rendering: https://www.youtube.com/watch?v=bcaqzOUv2Ao
- J. Lengiewicz, M. Kursa, P. Hołobut, Modular-robotic structures for scalable collective actuation, Robotica, Vol.35, No.4, pp.787–808, 2017.
- J. Lengiewicz, P. Hołobut, Efficient collective shape shifting and locomotion of massively-modular robotic structures, Autonomous Robots, Vol.43, No.1, pp.97–122, 2019.
- B. Piranda, P. Chodkiewicz, P. Hołobut, S. Bordas, J. Bourgeois, J. Lengiewicz, Distributed prediction of unsafe reconfiguration scenarios of modular-robotic Programmable Matter, 2020, preprint available at http://arxiv.org/abs/2006.11071.
- M. Yim, W. Shen, B. Salemi, D. Rus, M. Moll, H. Lipson, E. Klavins, G.S. Chirikjian, Modular self-reconfigurable robot systems, IEEE Robotics Automation Magazine, Vol.14, No.1, pp.43–52, 2007.
- P. Thalamy, B. Piranda, and J. Bourgeois, A survey of autonomous self-reconfiguration methods for robot-based programmable matter, Robotics and Autonomous Systems, Vol.120, p.103242, 2019.
- J.W. Suh, S.B. Homans, M. Yim, Telecubes: Mechanical design of a module for self-reconfigurable robotics, Proceedings of the IEEE International Conference on Robotics and Automation, 11–15 May 2002, Washington, DC, USA, pp.4095–4101, 2002.
- B. Piranda and J. Bourgeois, Designing a quasi-spherical module for a huge modular robot to create programmable matter, Autonomous Robots, Vol.42, No.8, pp.1619–1633, 2018.
- P.C. Foster, N.J. Mlot, A. Lin, and D.L. Hu, Fire ants actively control spacing and orientation within self-assemblages, Journal of Experimental Biology, Vol.217, No.12, pp.2089–2100, 2014.
- Fire ant movie: https://www.youtube.com/watch?v=NpiDADw5Omw
- Fire ant website at Georgia Tech: http://www.antphysics.gatech.edu/
- Slime mould movie: https://www.youtube.com/watch?v=5h8WOWEqP6o
- Programmable Matter consortium: https://www.programmable-matter.com/