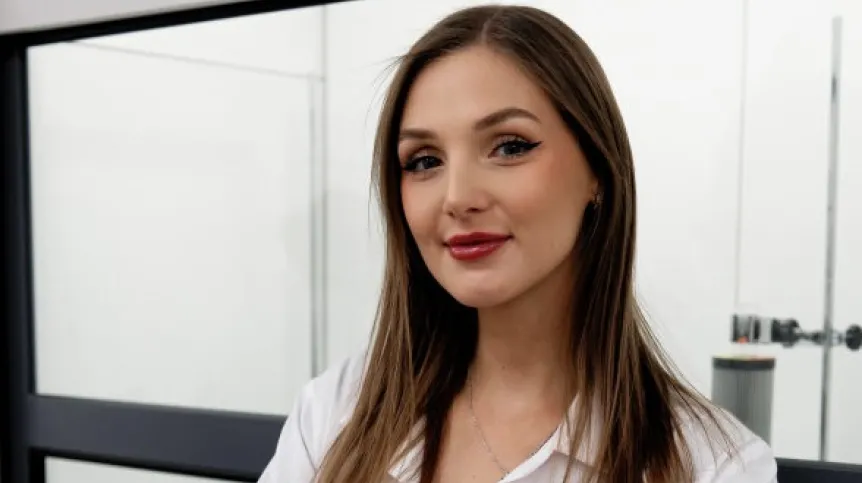
Scientists from the Cracow University of Technology are working on a bioactive material that can be used to print bone implants tailored to the individual needs of a given patient, especially the facial bones.
The university’s Dagmara Słota, who is establishing her first research team as part of the Polish National Centre for Research and Development LIDER program, spoke to PAP - Science in Poland about an implant resembling natural bone tissue, which will stimulate bone-forming cells to multiply.
She explained that bone defects or reconstructions are currently treated mainly with autogenous or allogeneic grafts. In the former case, a fragment of the patient's own bone is taken from an area of the body of low aesthetic importance. Then, this fragment should be reshaped to fit the defect and implanted in the place of defect. In turn, an allogeneic transplant involves collecting bone material from a donor, most often a deceased person, and the donor and recipient must have compatible antigens. 'After such a transplant, the patient should still take immunosuppressive drugs. Immunological complications may also occur. Moreover, waiting for a donor often requires patience and time,’ she said.
According to the biotechnologist, there are also commercial implants available on the market, but they are most often made of metals and carry the risk of corrosion. Such a personalised metal implant is also expensive because it requires the production of a separate mould for each patient.
Scientists decided to compose a material (along with the technology for obtaining it) that could ultimately be used to 3D print personalised bone tissue implants.
'We want to initially focus on facial bone implants. Not only aesthetic aspects are important here, such as restoring the symmetry of facial contours, but also the impact of the new material on bone function - such as the function of the eye socket, eating or speech. The skull is also responsible for protecting the most important organ of the human body - the brain, which is the centre of the nervous system. All this outlines our goal, which is to develop a material for 3D printing bone implants,’ Słota said.
Materials that come into contact with living organisms must be tested on a large scale. The scientists will strive to ensure that the implant has strength or hardness similar to natural bone. In vitro tests are planned, i.e. in glass in a simulated biological environment, and ultimately in vivo safety will be verified.
'We want our material to have some new features compared to other, currently available bioprinting materials. One of the assumptions is bioactivity. This means that the implant will stimulate bone-forming cells to multiply, which will translate into faster recovery for the patient. The phase composition of the material is also supposed to resemble natural bone tissue. It will be slightly porous and this will allow blood vessels to grow into it, which will minimize the risk of displacement. There are many plans, but I believe that they will all be realised,' Słota added.
The researcher is convinced that 3D printing personalised, innovative implants will enable patients to undergo a faster procedure, thus shortening the waiting time.
'The procedure of preparing a 3D model of the implant itself begins with imaging the shape and dimensions of the defect that is to be filled. This is usually done using an X-ray computed tomography or magnetic resonance imaging. The implant is then printed and the patient can undergo surgery. This shortens the entire procedure to just a few days. Therefore, it will be possible to quickly perform the procedure of implantation of a personalized implant, which, by stimulating bone-forming cells, will translate into faster recovery,’ said leader of the team, which also includes a nanotechnologist, an automation and robotics engineer, and specialists in 3D printing, medical microbiology, immunology and laboratory diagnostics, as well as materials and biomedical engineers.
Słota admitted that in medical practice there are already known attempts to implant personalised 3D printed implants. In the case of such an implant, the patient should also take medications that prevent the body from rejecting it; the type, dose and duration of taking the medication is determined by the doctor.
The biotechnologist added that the innovation in her project will be the composition of the material and its ability to accelerate regenerative processes.
She said: ’The implant will be based on polymers that will be appropriately modified to increase bioactivity,’ and added that the details of the implant's composition must remain a secret because there is no material on the market yet with the composition she and her group members have designed.
PAP - Science in Poland, Karolina Duszczyk
kol/ bar/ kap/
tr. RL