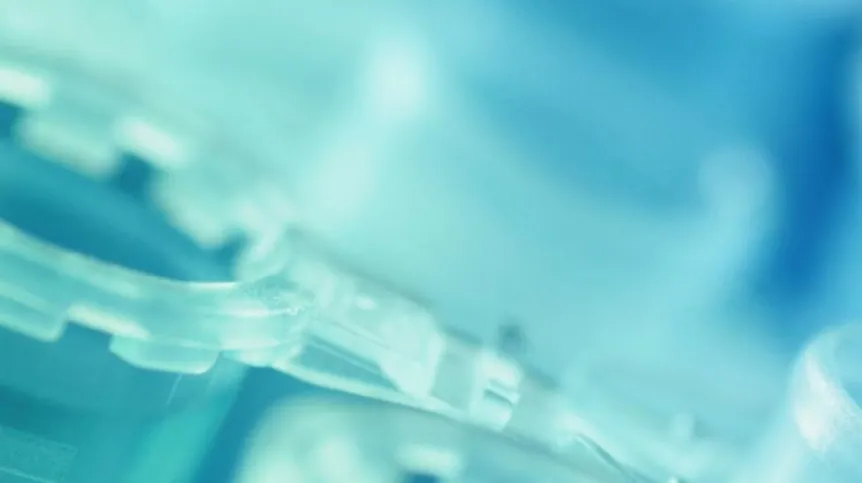
Chemical recycling is a type of recycling that makes it possible to obtain pure compounds for the production of polymers and further products from plastics. Now, Dr. Patrycja Maria Jutrzenka Trzebiatowska from the University of Gdańsk has added a new dimension - complex, 3D structures called MOFs.
Polish Press Agency: What does the project you have started involve?
Patrycja Maria Jutrzenka Trzebiatowska from the Faculty of Chemistry of the University of Gdańsk: I intend to chemically recycle several types of plastics. The plan is to recover monomers, i.e. basic elements from which plastics are made, from polyurethane (PU), polyethylene terephthalate (PET), polycarbonate (PC) and other materials. We will make MOFs (Metal-Organic Frameworks), which are organometallic structures.
PAP: This sounds quite complicated. What is chemical recycling? Is it different from 'ordinary' recycling?
P.J.T.: It differs significantly. Standard recycling mainly uses mechanical methods. After segregation and cleaning, bottles, packaging or other products are converted into granules, which can be re-used as a raw material for the production of plastic products.
PAP: And what about chemical recycling?
P.J.T.: This method goes one step further. We will break down polymers, or plastics, into monomers, into molecules that are basic components of these materials. Currently, they are produced in refineries, primarily from crude oil. We want to obtain them from processing used plastic items. The obtained compounds will be used to produce appropriate polymers and from them, depending on the material, items like bottles, fleece sweatshirts or mattresses can be produced.
PAP: What advantage does this approach have over standard recycling?
P.J.T.: The main limitation of mechanical recycling is that a material can only be processed 6-7 times. Later, the quality of the output material decreases and it ceases to meet relevant standards, e.g. regarding strength and visual parameters. However, if we obtain basic compounds with a chemical method, we obtain a fresh raw material for the production of plastics, the same material that is obtained from oil. However, I must say that although the assumptions seem simple, the matter is complex and that is why commercial chemical recycling practically does not exist yet.
PAP: Using MOFs, organometallic structures, is expected to be a step in this direction?
P.J.T.: They can be used in one of the two main types of chemical recycling, where they have the potential of acting as catalysts. With their help, the substances generated at intermediate stages can be broken down into the final product, i.e. monomers. Without suitable catalysts it would not be feasible, or only possible under difficult reaction conditions (very high temperature, elevated pressure), or it would take so long that it would be pointless. It must be noted that the variety of plastics is huge and different materials require different reactions and catalysts.
PAP: MOFs themselves are basically also a novelty...
P.J.T.: They have only been developed for about 20 years. These are complex 3D structures, and many different metals and organic chains can be used to synthesize them, which allows us to find those that will have high catalytic activity. MOFs are characterized by high reactivity towards activating C-H bonds, which is a key property for effective polymer degradation. Therefore, they can be used as catalysts.
PAP: Will you work on new MOFs?
P.J.T.: No, because over 20,000 types have already been created, and the development of a new type would require a separate research project. Perhaps a new type will be created during the research, but the novelty will primarily consist of using these substances in chemical recycling.
So far, one publication has been published on using MOFs (3 different ones) as catalysts in chemical recycling
PAP: You mentioned that this type of commercial processing of plastics practically does not exist yet. Could you tell us more about the current situation?
P.J.T.: This field is only at the beginning of its development. The first companies are interested in it, but among them are large corporations such as BASF, Henkel, or Coca-Cola. There was a company in Poland that tried to process plastics from bed mattresses in this way. One of the obstacles to rapid development of such a technology is that oil is still relatively cheap. At the same time, oil processing technologies are perfectly refined. This means that it is possible to obtain cheap industrial monomers from oil, the same ones that we want to recover from already produced plastics.
PAP: But ultimately we will run out of oil, and in the meantime we are dealing with a growing problem of plastic waste.
P.J.T.: I honestly believe that with chemical recycling, we can use what we have already produced, and use it again, without exploitation of raw materials, such as crude oil. Products that civilization has already produced are really abundant and with appropriate technologies we can obtain good quality raw material from them. Waste storage should be a last resort, because with proper segregation waste can be easily processed with mechanical recycling, or used to obtain basic substrates with chemical recycling.
PAP: Does your project have a good chance of being transformed into a commercial venture?
P.J.T.: During my doctorate, I patented a method associated with chemical recycling. A similar method developed by scientists at the Gdańsk University of Technology has been licensed by a company (the company bought a license for an earlier patent prepared at the Gdansk University of Technology). The use of MOFs on this field is new, so there is certainly patent potential. Whether it will translate into commercialisation, it's hard to tell at this point, but the planned research will certainly be a step in this direction.
Interview by Marek Matacz
PAP - Science in Poland
mat/ ekr/ kap/
tr. RL